ルーレット鋳鉄部品の鋳造プロセス
中厚板冷却床の圧延板の鋳造工程と材質の研究を通じて、金属樹脂砂コアを複数積み重ねたルーレット鉄鋳物の新しい製造方法を研究している。 この方法は、単純なプロセス、高い生産性、高い鋳造総合性能、および優れた表面品質を備えています。
ルーレット鋳鉄部品の鋳造プロセスの現状
ルーレットの鋳鉄部品とは、直径が高さよりもはるかに大きいタイプの鋳物を指します。 一般に、中間軸穴の加工要件は比較的高く、ハブとリムは厚く、スポークの壁は薄いため、温度差や温度差が大きくなりやすい。 ハブとリムはXNUMXつのホットスポットです。 鋳造プロセスが不合理である場合、鋳造は収縮空洞、収縮多孔性および亀裂欠陥を起こしやすい。 現在、ほとんどの国内メーカーは、通常の粘土砂型鋳造、一体鋳造、接線ゲート射出、およびハブで冷鉄と組み合わせて使用されるライザー供給または鋳造方法を使用してルーレット鋳造を製造しています。 この方法は大きなスペースを占め、プロセスの歩留まり、歩留まり、生産効率が低く、鋳造物の表面品質が悪い。
ルーレット型鉄鋳物冷却床ローラー(5700個以上)の製造作業を受けた後、最初に解決すべき問題は鋳造プロセスの研究です。 鋳造に不慣れな作業者が操作できるように、プロセスは単純である必要があります。 成形・注湯面積を削減し、既存の生産条件での生産ニーズに対応する必要があります。 鋳造工程を研究していると、再び材料の問題に遭遇しました。 作られたロールプレートは非常に脆く、生産にはまったく使用できませんでした。 鋳造工程と鋳造材料の研究を通じて、ルーレット鋳鉄部品の新しいタイプの鋳造工程が研究され、適格なローラーが製造されました。
主な研究内容と主要技術
1.材料研究
ローラープレートは、冷却床装置の重要なコンポーネントの5つです。 優れた表面品質と高い耐熱性が必要です。 鋳鉄の耐熱性は、主にその高温耐酸化性(すなわち、鋳鉄の表面に形成された酸化膜が保護効果を有するかどうか)および鋳鉄の成長(すなわち、サイズの不可逆的な膨張)に依存します。高温で動作する鋳鉄部品の)。 これらの2.30つの特性は、鋳鉄の化学組成と密接に関連しています。 鉄鋳物の強度と耐衝撃性は主に合金元素の数に依存するため、鋳物の材質の研究は非常に重要な問題になります。 このため、材料の研究を行い、化学組成を合理的に選択しました。これにより、鋳物の耐熱性が向上するだけでなく、鋳物の機械的特性も保証されます。 ローラーの元の設計材料はRQTSi2.89であり、その化学組成(%)は次のとおりです。wC= 4%〜5%、wSi = 5.5. 0.50%〜0.77%、wMn = 0.06%〜0.09%、wP = 0.062%〜 0.089%、wS = 0.38%〜0.49%、wCr = 140%〜220%。 その機械的特性は次のとおりです。引張強度160-270MPa、硬度750-900HBW。 最高作動温度は5〜3.05℃です。 この材料のシリコン含有量が高いため、鋳鉄の脆性転移温度が上昇します。 そのため、鋳物は非常に脆く、肉厚が不均一な脆性部品の製造には適していません。 ローラープレートはこの構造の鋳造に属しています。 その結果、生産は始まったばかりです。 当時、多くの廃棄物は物質的な問題によって引き起こされていました。 さらに、RQTSi3.51の材料はもろく、歩留まりが低いため、ほとんどの国内メーカーはローラーの製造にこの材料を使用していません。 以上のことから、ロールプレートの一括解体を回避し、中厚板プロジェクトの円滑な開始を図るため、ロールプレート製造用の新素材の試作を最優先事項としています。 多くの実験とデモンストレーションを通して、私たちは開発した新しい材料を使用することにしました。 その化学組成は、wC = 2.9%〜3.5%、wSi = 0.24%〜0.56%、wMn = 0.05%〜0.09%、wP = 0.010%〜0.030%、wS = 0.29%〜0.6%、wMo = 580%〜です。 695%。 その機械的性質は次のとおりです:引張強さ8〜18MPa、伸び210%〜280%、硬度750〜900HBW。 最高作動温度はXNUMX〜XNUMX℃です。 開発された材料の優れた特性と高い歩留まりにより、ユーザーに認められています。
材料を決定した後、材料の成分、球状化プロセス、接種剤と接種プロセス、炉の前での品質管理などに取り組み、成功しました。 ローラーの機械的特性は、鋳鉄工房の歴史の中で最高に達しました。 レベル。
2.製錬プロセスにおける重要な問題への取り組み
化学組成を決定した後、高品質の溶鉄を得るには、合理的な製錬プロセスが必要です。 耐熱ダクタイル鋳鉄の場合、球状化処理が特に重要です(つまり、接種剤と球状化プロセスの選択)。 球状化が処理されるとき、鋳物の機械的特性も良好です。 研究により適切な接種材料を選択し、合理的な球状化プロセスを開発しました。これにより、溶銑を十分に球状化できるため、鋳物の強度が向上するだけでなく、伸びも向上し、効果は非常に良好です。
- 球状化剤の選択球状化剤の品質は、球状化効果に直接影響し、溶銑や鋳物の品質に影響します。 多くの実験と実証を通じて、球状化剤はReMg5-8軽希土類を採用し、接種剤は75SiFeを採用し、鋳鉄の強度と伸びを大幅に向上させることができる独自の長時間作用型接種剤を採用することを最終的に決定しました。
- 球状化高品質の鋳造品を得るには、接種材料の選択と球状化プロセスも非常に重要です。 重要な問題に取り組むことで、適切な接種剤を選択し、合理的な球状化プロセスを策定しました。これにより、鋳造物の強度が向上するだけでなく、伸びも向上し、効果は非常に良好でした。
球状化プロセスではダムバッグを使用しますが、これは完全に乾燥させる必要があります。 さまざまな合金を予熱する必要があります。 ダムバッグに下から上に追加される合金は、軽希土類合金1.8%→接種剤0.8%→カバー鉄板または鉄粉(溶鉄温度による)→アルカリ表面0.5%です。 鉄の2/3を叩き、反応終了後、再度必要量まで叩き、流れに合わせて0.6%のフェロモリブデン、0.6%の接種剤を加え、スラグを除去します。
3.鋳造工程における重要な問題への取り組み
当社では、高品質なプロジェクトを実現するために、ローラーの表面品質、寸法公差、加工量について、国家標準よりも高い要件を提示しています。 ただし、ローラーには大量のバッチと厳しいスケジュールがあります。 スケジュールをつかむために、ワークショップはいくつかの鋳造技術を使用しなければなりませんでした。 なじみのない臨時職員がロールディスクを製造するため、ロールディスクのプロセスに非常に高い要件が課せられます。 鋳造工程の研究を行っています。
- モデリングプロセスの研究部品の構造から、ハブが厚く、スポークが細いことがわかります。 現在、ほとんどの国内メーカーは、ハブとタンジェンシャルゲートにライザーを備えた通常のサンドタイプの一体型鋳造を使用して、この構造の鋳造品を製造しています。 このプロセスでは、プロセスの歩留まり、完成品の割合が低く、生産効率も低くなります。 通常の砂型を一体鋳造に使用する場合、必要な時間内に5,700本のロールの生産を完了し、毎日144本のロールを生産する必要があり、288個のサンドボックス、16個の金型、および十分な成形と注入領域があります。必要であり、職人技コンプレックスは、鋳造に不慣れで、生産要件を満たすことができない労働者のために操作することができません。 そのために、金属樹脂砂コアの積み重ねプロセスを比較して選択しました。つまり、金属コアボックス樹脂砂を使用してコアを作成し、次に砂コアを一緒に落とし、ボックスリングに置いて注ぎます。 このプロセスを採用することにより、生産ニーズを満たすために必要な金属コアボックスは8セットのみです。 各スプルーは3スタックで注がれ、各スタックは8ピースで注がれ、底板は同時に48ピースで注がれます。 共通ゲート方式を採用しているため、鋳造率が高く、レジン砂型鋳造品の表面品質は良好です。
- 工具の設計と製造プロセスが決定された後、必要な工具を設計および製造しました。
- コアサンドのプロポーショニング、ミキシング、生産。 コアサンド準備プロセスは、レジンサンドアセンブリコアスタッキングプロセスの鍵です。 製造当初は、樹脂と硬化剤の比率が不適切であったため、金型から砂芯を取り除くことが難しく、砂芯の表面品質が非常に悪かった。 比率の試行生産により、最終的に樹脂、養生剤、生砂の比率が決定され、適格な砂コアが生産されました。比率:0.45〜0.224mm(40/70メッシュ)のスクラビングサンド100%、樹脂は1.8%〜2%生砂重量、硬化剤は樹脂の30%〜-50%混合:S2512Cサンドミキサーを使用して樹脂砂を混合します。 秤量した生砂をサンドミキサーに加え、硬化剤を加え、8〜10分間混合を開始し、樹脂を加え、8〜10分間混合して粉砕し、砂を出力します。砂コアの製造:拭き取りコアボックスの内面は製造前にきれいにし、離型剤を塗布し、コアを作るときに砂を均等に叩き、コアを修理するときにサイズが正確であることを確認します。 準備されたコアには順番に番号が付けられ、アルコールベースのグラファイトが使用されます。 ペンキをXNUMX回磨きます。 塗料に着火したら、乾いた布で砂芯の表面をなめらかに磨きます。
- 注湯システムの選択注湯システムのサイズは、鋳物の品質に直接影響します。 注湯システムの面積が小さすぎると、不十分な注湯や防寒壁などの欠陥が簡単に形成されます。 大きすぎると鋳物からの洗浄が困難になります。 鋳物はダクタイル鋳鉄でできています。 最初に生産を開始したとき、シャフトのヘッドに4つの内部ランナーを設置しました。 その結果、ゲートの清掃によりローラーディスクが廃棄されることが多かった。 その後、鋳物の形状と重量に基づいた実験を通じて合理的なゲートシステムを選択し、適格な鋳物を製造しました。 黒鉛化膨張と自己供給特性を最大限に活用し、非ライザー供給方式の鋳造を採用しています。 各ローラーのヘッドには、80mm×40mmのフラットゲートがXNUMXつだけ開いています。 この注湯システムは、溶銑を節約するだけでなく、注湯ライザーの洗浄工数を削減し、鋳物の表面品質も良好です。
- スタッキングローラーの数の決定スタッキング注入技術を使用して、毎回注入される鋳物の数は、鋳物の品質に直接影響します。 鋳物が多すぎると、送りが不十分なために穴が収縮する傾向があります。 鋳造品が少なすぎると、労働生産性とプロセス歩留まりが低すぎます。 研究チームが試作を開始したときの品質を確保するために、スタックごとに6個だけが注がれました。 生産経験の継続的な蓄積により、慎重な計算によれば、現在、スタックごとに8個、3スタックごとにXNUMX個のスプルーを注いでいます。 その結果、鋳造品の品質を保証するだけでなく、労働生産性も向上します。
- 注湯温度の選択。 注湯温度が高い鋳物は、気孔率や収縮などの欠陥が発生しやすく、注入温度が低すぎるため、表面の注湯不足や鉄豆などの欠陥が発生します。 実験により1280〜1300の適度な注入温度を設定しました。 ℃、適格な鋳物を製造します。
- ボクシング時間の管理。 ボクシングが早すぎると鋳物が変形しやすく、後の注入に影響します。 鋳物のサイズと量に応じて、ストライク時間は6時間と規定しました。
品質検査
製造されるローラーの品質を保証するために、厳格な検査システムを確立しました。各ローラーには鋳造テスト用のテストブロックを取り付ける必要があり、テストブロックの機械的特性、金属組織構造、化学組成は100%テストされます。 。 資格のないものは工場を出ません。
生産効果
- 金属樹脂サンドコアアセンブリのマルチグループスタッキングプロセスによって開発されたローラーディスクは、高強度と優れた表面品質を備えています。 その様々な特性は、元のデザイン素材をはるかに超えており、ユーザーのニーズを満たしています。
- このプロセスを採用した後、砂と鉄の比率はわずか1.5:1であり、国内の先端技術レベル(3〜4.5):1よりもはるかに低く、多くの樹脂砂を節約できます。
- プロセスは操作が簡単で、品質が保証されています。 鋳鉄工房では、熟練していないオペレーターを多数使用して高品質のローラーも製造しました。
- 生産性がXNUMX倍以上向上し、工数を節約できるだけでなく、サンドボックスのコストも大幅に節約できます。
- 複数のローラーの複数のセットが共通の注入システムを使用し、ライザーが不要なため、鋳造歩留まりは95%と高く、通常のプロセス方法の70%の工程歩留まりよりもはるかに高くなっています。 ゲートシステムの断面積が小さいため、軽くハンマーで叩くだけで洗浄できます。これにより、鋳物の切断やライザーの注入にかかる工数が大幅に削減されます。
弊社製のロールプレートは中厚板工場で生産されて以来、順調に稼働しており、冷床の傷、鋼板の凹凸、ずれはありませんでした。ロールプレートの品質による鋼板。 効率性は、当社の工場の生産の通常の運用を保証し、優れた経済的利益を生み出します。
まとめ
ローラープレートの材質と鋳造工程の研究を通じて、ローラープレートの鋳造作業を時間通りに質と量で完了し、当社の中厚板プロジェクトを円滑に開始するための基礎を築きました。 このプロセスの高効率と鋳造品の優れた表面品質により、冷却ベッドロールの完成に基づいて、Lingang、Xianggang、およびその他のメーカーから20,000を超えるロール製造タスクを実施しました。 プロモーションとアプリケーションの見通しは広く、経済的です。 メリットは非常に重要です。
転載のためにこの記事の出典と住所を保管してください:ルーレット鋳鉄部品の鋳造プロセス
Minghe Casting Companyは、高品質で高性能な鋳造部品の製造と提供に専念しています(金属ダイカスト部品の範囲には主に次のものが含まれます) 薄肉ダイカスト,ホットチャンバーダイカスト,コールドチャンバーダイカスト)、ラウンドサービス(ダイカストサービス、CNCの機械化,金型製作、表面処理)。カスタムのアルミニウムダイカスト、マグネシウムまたはザマック/亜鉛ダイカスト、およびその他の鋳造要件については、お問い合わせください。
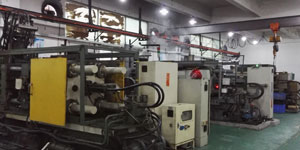
ISO9001とTS16949の管理下で、すべてのプロセスは、ブラスターからウルトラソニック洗濯機に至るまで、何百もの高度なダイキャスティングマシン、5軸マシン、およびその他の設備を介して実行されます。経験豊富なエンジニア、オペレーター、検査官のチームがお客様の設計を実現します。
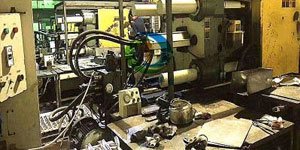
ダイカストの委託製造業者。 機能には、0.15ポンドからのコールドチャンバーアルミニウムダイカスト部品が含まれます。 6ポンドまで、クイックチェンジセットアップ、および機械加工。 付加価値サービスには、研磨、振動、バリ取り、ショットブラスト、塗装、メッキ、コーティング、組み立て、および工具が含まれます。 使用する材料には、360、380、383、413などの合金が含まれます。
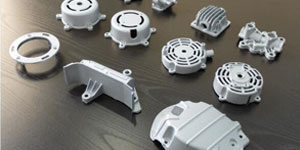
亜鉛ダイカスト設計支援/コンカレントエンジニアリングサービス。 精密亜鉛ダイカストのカスタムメーカー。 ミニチュア鋳造、高圧ダイカスト、マルチスライドモールド鋳造、従来のモールド鋳造、ユニットダイおよび独立ダイカスト、およびキャビティシール鋳造を製造することができます。 鋳物は、最大24インチインチ+/- 0.0005インチの公差で長さと幅で製造できます。
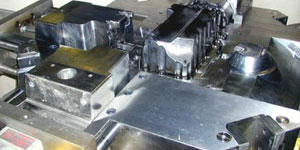
ISO 9001:2015年にダイキャストマグネシウムの認定メーカー。機能には、最大200トンのホットチャンバーと3000トンのコールドチャンバーの高圧マグネシウムダイカスト、工具設計、研磨、成形、機械加工、粉末および液体塗装、CMM機能を備えたフルQAが含まれます。 、組み立て、梱包、配送。
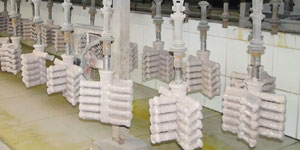
ITAF16949認定済み。 追加の鋳造サービスが含まれます インベストメント鋳造,砂型鋳造,重力鋳造, ロストフォームキャスティング,遠心鋳造,真空鋳造,永久鋳型鋳造、。機能には、EDI、エンジニアリング支援、ソリッドモデリング、および二次処理が含まれます。
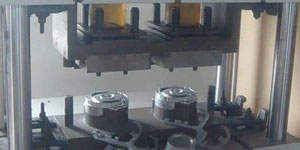
鋳造業 部品のケーススタディ:車、バイク、航空機、楽器、船舶、光学機器、センサー、モデル、電子機器、エンクロージャー、時計、機械、エンジン、家具、ジュエリー、ジグ、テレコム、照明、医療機器、写真機器、ロボット、彫刻、音響機器、スポーツ機器、工具、おもちゃなど。
次に何ができるでしょうか?
∇ホームページに移動 ダイカスト中国
By ミンゲダイカストメーカー |カテゴリ: 役立つ記事 |材料 タグ: アルミ鋳造, 亜鉛鋳造, マグネシウム鋳造, チタン鋳造, ステンレス鋼鋳造, 真ちゅう鋳造,ブロンズ鋳造,キャスティングビデオ,会社の歴史,アルミダイカスト |コメントオフ