バーミキュラー鉄生産のプロセス制御
ねずみ鋳鉄と比較して、バーミキュラー鉄の引張強度は少なくとも70%増加し、弾性率は35%増加し、疲労強度はほぼXNUMX倍になります。 アルミニウム合金と比較して、バーミキュラーアイアンの強度と剛性はXNUMX倍高く、疲労強度はXNUMX倍高くなっています。 バーミキュラーアイアンのこれらの特性は、エンジンがパワーウェイトレシオを改善し、シリンダー圧力を上げる可能性を提供します。 シリンダー圧力の上昇は、次世代の直噴ディーゼルエンジンの最適な性能の鍵です。 バーミキュラーアイアンの広範な用途に対応するために、鋳造業界は現在、バーミキュラーアイアンの生産を安定して信頼できるものにするために、積極的に準備、多額の投資、新しいプロセスの再構築を行っています。
試作品から量産までのバーミキュラーアイアンエンジンにとって、決定的な要因は品質リスクです。 高品質のバーミキュラーアイアンの場合、安定ゾーンは非常に小さく、マグネシウム含有量が0.008%の範囲にすぎません。 0.001%のマグネシウムが失われるなどの微量では、フレークグラファイトが生成され、機械的特性が25%から40%低下します。 この記事では、熱分析法に基づくプロセス制御システムについて説明します。 このシステムは、マグネシウムの損失を測定し、溶融鉄の状態をオンラインで調整して、フレークグラファイトの生成を防ぎます。 この測定と調整のオンライン制御方法は、バーミキュラーアイアンを製造するプロセスの変動性を最低点まで低減し、バーミキュラーアイアンの製造によって引き起こされる品質リスクを根本的に排除します。
高馬力、高トルク、低排気ガス、低燃費の需要は増え続けています。 これにより、高出力ディーゼルエンジンの設計者は点火ピーク圧力を上げる必要があり、エンジンの熱負荷と機械的負荷が大幅に増加します。 熱負荷と機械的負荷が同時に増加するため、現在使用されている従来の鋳鉄および合金鋳鉄(CrMo)エンジンは、使用上限に達しているか、上限を超えています。 エンジンメーカーは、より高い強度とより優れた耐熱性を備えた材料を必要としています。
バーミキュラーアイアンはすぐに人々に選ばれる素材になりました。 新世代トラックエンジンのシリンダーブロック、シリンダーヘッド、シリンダーライナーの信頼性を大幅に向上させます。 さまざまな特性(鋳造特性、機械加工特性、熱伝導率、機械的特性など)の最適な組み合わせを実現するには、これらの部品を0%〜20%の球状化率(80%〜100%のクリーピング率)で作成する必要があります。 )バーミキュラーアイアン製。 球状化率が20%を超えると、一連の不利な要因が発生します。 たとえば、収縮量が大きすぎるため、シリンダーヘッドなどの複雑な形状の部品は特に収縮しやすくなります。 もう0つの例は、機械加工中の過度の摩耗による工具寿命の低下です。 また、熱伝導率が大幅に低下し、熱応力などが発生します。 バーミキュラーアイアンのもう一方の端では、フレークグラファイトの出現により、機械的特性が直線的に低下し、エンジンが新しい要件を満たすことができなくなります。 要約すると、新世代のトラックエンジンのニーズを満たすために、高強度バーミキュラーアイアンの球状化率は20%から80%の間でなければなりません(つまり、クリープ率はフレークなしでXNUMX%を超えます)。
製造工程管理を使用するかどうかは、製品の年間生産量、製品の複雑さ、および金属組織の変化の許容範囲によって異なります。 図1に示すように、インゴットモールドなどの比較的単純で少量の部品は、通常、従来の鋳造方法で製造できます。 プロセス制御は一般的に必要ではなく、経済的に費用効果が高くありません。 エキゾーストパイプ、クランクスリーブ、ブラケットなどのコンポーネントの年間生産量が増加する場合、プロセス制御を導入することは理にかなっているはずです。 このタイプの製品は年間生産量が多いですが、鋳造の年間トン数は高くありません。 金属組織の要件はそれほど厳密ではなく、球状化率を50%まで高くすることができます。 また、このような部品の機械加工が少ないため、生産に追加できるチタンの増加により、制御範囲を拡大することができます。 このタイプの製品の場合、従来の鋳造方法と厳格なトレーニングは、一般的にバーミキュラーアイアンの生産に適しています。 しかし、品質管理の観点からは、プロセス管理はより安全でなければなりません。 同様に、プロセス制御は、大型の船舶用エンジンブロックとシリンダーヘッドの製造を保証します。 サイズが大きく、生産量が少ないことは製品の製造に役立ちますが、標準を超える製品によって引き起こされる経済的損失は、一連のプロセス制御システムを追加するのに十分です。
プロセス制御を最も必要とする製品は、自動車のエンジンシリンダーブロック、シリンダーヘッド、ブレーキディスクで、年間生産量が多く、複雑さが高く、技術的要件が厳しいものです。 これらの製品の年間生産量と年間トン数は非常に高いです。 それらはサイズが複雑で、金属組織構造を要求し、収縮空洞を生成する傾向があります。 これらの製品には品質リスクがあってはなりません。そうでないと、損失は非常に深刻になります。
エンジンブロック、シリンダーヘッド、シリンダーシートの性能に関する厳しい要件が、製品仕様の製造の基礎を築きました。 キャスタビリティ、機械加工性、機械的特性の最高の包括的な性能を得るには、スフェロイド化率はコンポーネントのすべての主要部分で0%から20%の範囲でなければなりません。 さらに重要なことに、局所的な弱さによって引き起こされる部品の損傷を防ぐために、フレークグラファイトは絶対に避けなければなりません。 良好な機械的添加性を達成するために、遊離炭化物を最小限に減らす必要があります。 したがって、チタンは絶対に添加しないでください。 最後に、生産の観点から、鋳造所は、金属組織構造によって引き起こされる最低のスクラップ率を確実にするために、安定した信頼できるプロセスを必要とします。 自動車産業の製造業者は品質保証を必要とし、鋳造品の100%が金属組織学的要件を満たさなければなりません。 シリンダーブロック、シリンダーヘッド、シリンダーシートの大規模で信頼性の高い生産には、注ぐ前のプロセスの変動を排除するために、溶融鉄の正確な分析とオンライン調整が必要です。
バーミキュラーアイアンの安定性
圧縮鉄が複雑な部品(エンジンブロックなど)を製造するために大量に使用されない理由は、圧縮鉄の安定領域が小さすぎて、製造のリスクがないことを保証できないためです。 一般的に言えば、この安定ゾーンは、図0.008に示すように、2%のマグネシウムの領域にのみ広がります。安定ゾーン内のプラットフォームのサイズと位置は、製品によって異なります。 実際、利用可能なマグネシウムの範囲はこれよりも小さいです。 5分ごとに、活性マグネシウムは0.001%燃焼するためです。 溶銑の最初の注入点は、最終鋳造部品にフレークグラファイトが現れないように、圧縮鉄からねずみ鋳鉄への鋭い転換点から十分に離れている必要があります。 溶鉄にマグネシウムを加えると、約15分でフレークグラファイトが現れます。
開始点は、安定したプラットフォームの右側に近すぎないようにする必要があります(マグネシウム含有量が高い)。そうしないと、薄い部分と急冷部分に大量の球状黒鉛が形成されます。
利用可能な小さなプラットフォームエリアに加えて、プラットフォームエリアは常に動いています。 活性酸素と硫黄の含有量が高い場合、それらはより多くの活性マグネシウムを消費し、プラットフォーム全体が右に移動します(マグネシウム含有量が高い)。 逆に、活性酸素と硫黄の含有量が少ない場合、プラットフォームは左に移動します(マグネシウム含有量が少ない)。 原料の組成、純度、酸化度、湿度などの変化により、一定の化学組成で鉄を制御することができなくなります。
バーミキュラーアイアンからねずみ鋳鉄への変換では、活性マグネシウムを0.001%減らすだけで済みますが、マグネシウムの燃焼によって部品全体がフレークグラファイトになるわけではありません。 活性マグネシウムが十分でない場合、グラファイトは最初にフレークを形成し、固化するにつれて外側に膨張し、マグネシウムはたるんで固液界面の前端に集中します。 活性マグネシウムの初期量が適切である場合、図3に示すように、共晶の境界にバーミキュラーグラファイトが形成されます。フレークグラファイトは、最初に散在するフレークグラファイトスポットとして現れます。 すべての一般的なフレークグラファイトとは異なり、これらの孤立したフレークグラファイトスポットは超音波で検出するのが困難です。 それらが超音波でスキャンされる可能性は高くありません。
マグネシウムのバーミキュラー鉄に対する感度を図4に示します。10トンの溶銑取鍋に25グラムのマグネシウムを加えるだけで、Φ300テストサンプルに分散したフレークグラファイトスポットをバーミキュラーグラファイトに完全に変換できます。 フレークグラファイトスポットを備えたテストバーの引張強度はわずか450MPaですが、完全な沿面距離を備えた同じテストバーの引張強度はXNUMXMPaに達します。
図5に示すように、接種剤はバーミキュラー鉄の安定したプラットフォームにも非常に敏感です。80トンの溶融鉄に25グラムの接種剤を追加すると、Φ3テストバーの球状化率が21%からXNUMX%に増加します。 接種量が多く、結晶核が多く、球状黒鉛の形成につながる。 これにより、バーミキュラーアイアンプラットフォームが高い球状化率の方向に上昇します。 接種率が低いと、プラットフォームが下に移動します。 溶銑の過熱温度、保持時間、原材料の化学組成、接種材料の種類、接種量などの多くの要因が、バーミキュラー鉄プラットフォームの位置に影響を与えます。
プロセス制御技術の最も基本的な要件は、溶鉄の状態を正確に測定および分析することです。 バーミキュラーアイアンの場合、信頼性の高い生産管理には、クリープアッシュ遷移からの活性マグネシウムの臨界点、その後のマグネシウムの燃え尽きの程度、および接種の程度を同時に測定する必要があります。
球状化と接種後、Xinteプローブを溶鉄に挿入することにより、200グラムの熱分析サンプルが得られます。 XNUMX秒間の挿入プロセス中に、プローブ壁と溶鉄は熱平衡状態に達します。 従来の熱分析サンプルカップとは異なり、この薄肉サンプラーは毎回同じサンプル量を保証するだけでなく、サンプルカップに注がれる溶鉄の酸化を防ぎます。 従来の熱分析では、激しい結露などの現象が発生しないため、過熱度の測定がより正確になります。
図6aに示すように、Xinteプローブはプレスされた延伸鋼板でできています。 基本的には球形の容器です。 溶鉄を含む薄い鋼の壁には、魔法瓶のような断熱層があります。 断熱層の厚さは高さ方向に応じて対称的に厚くなり、周囲への均一な熱放散と冷却を確保し、その中の鉄のzz水は球体の凝固に近いです。 プローブの保護チューブには100つのN型熱電対があります。 熱電対は、測定のたびに引き出して、6回以上繰り返し使用できます。 XNUMXつの熱電対のXNUMXつはコンテナの下部にあり、もうXNUMXつはコンテナの熱中心にあります。 容器は球形で自由に吊り下げられているため(これは、熱吸収ブラケット上にある従来の熱分析サンプルカップとは異なります)、図XNUMXbに示すように、溶鉄は容器内に均一な熱流を生成します。 この熱流により、溶鉄が容器内で継続的に交換され、プローブの下部に流れの仕切りが形成されます。
注ぐ際の溶鉄の自然な損失を模倣するために、活性マグネシウムと反応するコーティングがプローブ壁にあります。 溶銑は、熱流によって駆動されてコーティングされた壁に沿って流れます。 反応後、溶鉄のマグネシウム含有量は減少し、容器の底のコンパートメントに蓄積します。 直接言えば、プローブの中央にある熱電対は、注入の初期状態である未反応の溶鉄を測定します。 下部の熱電対は、注入終了後の状態を測定します。 反応性コーティングの配合は非常に特殊です。 コンパートメントに蓄積された溶銑が中央の溶銑よりも0.003%活性が低いことを正確に確認する必要があります。 したがって、初期のマグネシウム含有量がクリーピングアッシュの転換点に近すぎると、コンパートメント内の溶鉄がねずみ鋳鉄を生成します。これは、この領域の熱電対によって測定されます。 このようにして、鋳造の開始時に、ワークショップはマグネシウムをさらに追加して、避けられないマグネシウムの燃焼損失を相殺することができます。
下部の熱電対がバーミキュラーアイアンカーブを示している場合は、初期マグネシウム含有量が十分に高いため、鋳造終了後にフレークグラファイトが存在しないことを示しています。
図7は、サンプル測定後のXinteプローブの断面侵食図です。 この図では、パーティション領域、メインサンプル領域、および熱電対保護チューブがはっきりとわかります。 活性マグネシウムが0.003%減少すると、分離ゾーンにD字型のグラファイトとフェライトマトリックスが形成されます。 下部のフレークグラファイト領域のサイズは、メインサンプル領域の初期マグネシウム含有量を直接反映しています。 このゾーンのサイズは、下部で放出される熱から計算できます。 熱放出とパーティションのサイズの間の変動係数回帰は0.9を超えており、これはXNUMXつの間の関係が非常に近いことを証明しています。 放出される熱は、冷却曲線の時間積分によって得られます。 現在の溶銑と注湯終了時の溶銑の状態を同時に測定するこの方法は、注湯前のマグネシウム含有量の精度を保証します。
バーミキュラーアイアンは球状化剤や接種剤に非常に敏感であるため、鋳造所がねずみ鋳鉄やダクタイル鋳鉄の製造に使用される過剰な処理方法を使用することは不可能です。 図8に示すように、バーミキュラーアイアンはその感度により、マグネシウムプラットフォーム領域だけでなく、正方形のウィンドウ内でのみ安定します。 信頼性の高いバーミキュラー鉄製造プロセスでは、金属組織が目標を確実に満たすように、最初から最後まで球状化と接種を制御する必要があります。
どんなに努力しても、どんなに厳しく管理しても、溶銑の変動は避けられません。 溶銑処理について人々がどれほど正確に知っているかは言うまでもなく、サンドイッチ法などのワンステップ処理方法では、各処理が狭いバーミキュラー鉄ウィンドウ内に収まるとは限りません。 混合比、炉温、保持時間、溶銑の予熱度、タッピング速度、タッピング溶融鉄のタッピング位置(測定の内側または外側)、タッピング溶融鉄の重量、合金バッグの状態、球状化剤などの多数の生産変数(PeSiMg)の実際のマグネシウム含有量、サンドイッチ法における各層の合金配置、および鉄くずの被覆率などはすべて、マグネシウムの吸収に影響を与えます。 これらの要因に加えて、活性酸素と活性硫黄の含有量も、バーミキュラー鉄窓のサイズと位置を変更します。 取鍋内の溶銑の滞留時間、輸送時間、注湯時間の変化はすべて、利用可能な燃焼時間を変化させます。
ただし、最も予測不可能な変動要因は、オペレーターのエラー、または異なる作業習慣による異なるオペレーター間の違いです。
大規模な大量生産では、処理後の溶銑の凝固特性を測定することが唯一の安全な方法です。 このようにして、バーミキュラー鉄窓のサイズ、位置、および合金吸収に影響を与えるさまざまな要因が包括的に測定、分析、および検討されてきました。 次に、適切な量のマグネシウムと接種剤を加えることができます。 溶銑の各取鍋は、理想的な状態にアップグレードされた後に注がれます。 このXNUMX段階の測定および調整プロセス制御方法は、生産のばらつきを最小限に抑え、鋳造におけるフレークグラファイトのリスクを完全に排除します。
溶銑取鍋によるバーミキュラー鉄生産のプロセス制御
図9に示すように、プロセス制御は、最初の球状化および接種処理後の溶鉄の熱分析から始まります。 分析結果によると、ワイヤ送給機は、マグネシウムと接種剤を添加するワイヤの長さを自動的に表示し、オペレータが開始するのを待ちます。 供給ラインが完了すると、取鍋はすぐに鋳造ラインに送られます。 測定と調整のプロセス全体には約XNUMX分かかります。 この期間中、ワークショップでは、スラグ除去などの従来の鋳造前処理を実行できます。 これにより、鋳造ラインの連続性が保証されます。
運転の観点から、生の溶鉄はマグネシウムを含まず、そのインキュベーション能力も非常に限られています。 球状化と接種の後、マグネシウムと接種剤は最初に溶鉄中の活性酸素と硫黄を食べ、次に溶鉄をボード上の特定の位置に「ジャンプ」させます。 図10の例では、溶鉄のマグネシウム指数と接種指数はそれぞれ65と45です。 シャドウ生成の主な変化パラメータは、測定および処理後の溶鉄に示されているため、熱分析の結果は、溶鉄の現在の状態を直接反映しています。 残っているのは、適切な量のマグネシウムと接種剤を加えて、溶鉄を現在の位置から必要な開始点まで上昇させることです。 図10の例では、最初に23ユニットのマグネシウムケーブルが追加され、次に100,000ユニットの接種ケーブルが追加されています。 インデックスユニットとケーブル長の対応する関係は、製品とワークショップに応じて調整され、プログラムでコンパイルされます。 5万近くのバーミキュラー鉄鋳物の過去の経験に基づくと、マグネシウムケーブルの平均追加量は12トンあたり50メートルです。 30メートルあたりXNUMXグラムのマグネシウムを含み、XNUMX%の吸収率で計算すると、溶鉄XNUMXトンあたりのマグネシウムの添加量はわずかXNUMXグラムです。 添加量が非常に少なく、初期処理で主な変更が行われているため、調整は非常に効果的で信頼性があります。 調整後、熱分析を行う必要はありません。
初期処理では、処理後の状態を初期注入位置より低くする必要があります。これにより、マグネシウムと接種剤の吸収に役立つすべての要素が最適値に達しても、溶鉄は初期注入状態にしか到達しません。 。 過剰処理しないことを除いて、処理後の溶銑はねずみ鋳鉄と白鉄の状態ではありません。 鋳造プロセスをより効率的にするために、溶融鉄の各取鍋のマグネシウム指数と接種指数がプロセスブロック図に表示されます。 ブロック図の変化傾向に応じて、オペレーターは次の取鍋に追加される溶鉄の量を調整できます。 炭素当量値も画面に表示されます。 これらのデータは編集されて本番ログに保存されているため、追跡して包括的にすることができ、品質保証の要件も満たしています。
熱分析とその後の調整により、バーミキュラーアイアンの生成を確実に行うことができますが、分析のために最終鋳造のスプルーカップからサンプルを採取することをお勧めします。 従来の品質検査と比較して、この熱分析結果はオンライン分析を提供し、必要に応じて鋳物を分類することができます。 プローブ内のマグネシウム損失のシミュレーションにより、この「非破壊」検査技術は、金属組織法や超音波法よりも効果的です。 この方法はより大きなサンプルサイズを測定するため、次の10〜15分で溶鉄がどのように固化するかも検出します。
総括する
プロセス制御システムの選択は、製品と鋳造プロセスによって異なります。 バーミキュラーアイアンエンジンカバーやシリンダーなどの複雑な製品を鋳造する場合、システムはマグネシウムと接種剤の含有量を同時に制御して、注入の最初から最後まで非常に狭いウィンドウ内に収まるようにする必要があります。 最高の鋳造性、機械的加法性、その他の包括的な性能と最高の使用機能を確保するには、球状化率を0%から20%(クリーピング率80%から100%)にする必要があります。 局所的な欠陥や弱点を防ぐために、フレークグラファイトスポットを完全に排除する必要があります。
プロセス制御システムの出発点は、溶鉄の状態を正確かつ効果的に測定することです。 信頼性の高い大規模なバーミキュラー鉄の生産には、プロセスの変更や人的操作のエラーを排除するための実行可能な制御方法が必要です。 プロセスの変化を排除する最も効果的な方法は、球状化と接種後に溶鉄の熱分析を行うことです。 熱分析の結果によると、注ぐ前に正確な量のマグネシウムと接種剤がさらに添加されます。 このオンライン測定および調整方法は、鋳造生産ラインの安定性を保証し、大規模なバーミキュラー鉄生産によってもたらされるさまざまなリスクを排除します。
転載のためにこの記事の出典と住所を保管してください: バーミキュラー鉄生産のプロセス制御
ミンゲ ダイカスト会社 高品質で高性能な鋳造部品の製造と提供に専念しています(金属ダイカスト部品の範囲は主に含まれています 薄肉ダイカスト,ホットチャンバーダイカスト,コールドチャンバーダイカスト)、ラウンドサービス(ダイカストサービス、CNCの機械化,金型製作、表面処理)。カスタムのアルミニウムダイカスト、マグネシウムまたはザマック/亜鉛ダイカスト、およびその他の鋳造要件については、お問い合わせください。
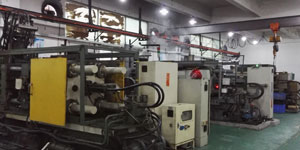
ISO9001とTS16949の管理下で、すべてのプロセスは、ブラスターからウルトラソニック洗濯機に至るまで、何百もの高度なダイキャスティングマシン、5軸マシン、およびその他の設備を介して実行されます。経験豊富なエンジニア、オペレーター、検査官のチームがお客様の設計を実現します。
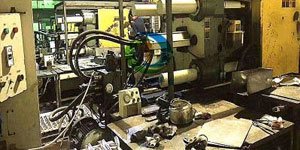
ダイカストの委託製造業者。 機能には、0.15ポンドからのコールドチャンバーアルミニウムダイカスト部品が含まれます。 6ポンドまで、クイックチェンジセットアップ、および機械加工。 付加価値サービスには、研磨、振動、バリ取り、ショットブラスト、塗装、メッキ、コーティング、組み立て、および工具が含まれます。 使用する材料には、360、380、383、413などの合金が含まれます。
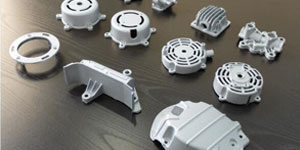
亜鉛ダイカスト設計支援/コンカレントエンジニアリングサービス。 精密亜鉛ダイカストのカスタムメーカー。 ミニチュア鋳造、高圧ダイカスト、マルチスライドモールド鋳造、従来のモールド鋳造、ユニットダイおよび独立ダイカスト、およびキャビティシール鋳造を製造することができます。 鋳物は、最大24インチインチ+/- 0.0005インチの公差で長さと幅で製造できます。
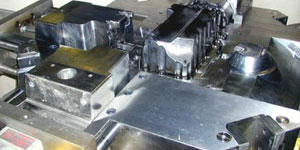
ISO 9001:2015年にダイキャストマグネシウムの認定メーカー。機能には、最大200トンのホットチャンバーと3000トンのコールドチャンバーの高圧マグネシウムダイカスト、工具設計、研磨、成形、機械加工、粉末および液体塗装、CMM機能を備えたフルQAが含まれます。 、組み立て、梱包、配送。
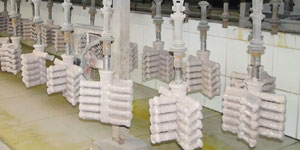
ITAF16949認定済み。 追加の鋳造サービスが含まれます インベストメント鋳造,砂型鋳造,重力鋳造, ロストフォームキャスティング,遠心鋳造,真空鋳造,永久鋳型鋳造、。機能には、EDI、エンジニアリング支援、ソリッドモデリング、および二次処理が含まれます。
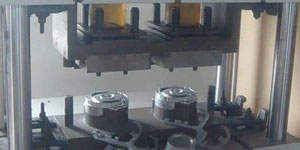
鋳造業 部品のケーススタディ:車、バイク、航空機、楽器、船舶、光学機器、センサー、モデル、電子機器、エンクロージャー、時計、機械、エンジン、家具、ジュエリー、ジグ、テレコム、照明、医療機器、写真機器、ロボット、彫刻、音響機器、スポーツ機器、工具、おもちゃなど。
次に何ができるでしょうか?
∇ホームページに移動 ダイカスト中国
By ミンゲダイカストメーカー |カテゴリ: 役立つ記事 |材料 タグ: アルミ鋳造, 亜鉛鋳造, マグネシウム鋳造, チタン鋳造, ステンレス鋼鋳造, 真ちゅう鋳造,ブロンズ鋳造,キャスティングビデオ,会社の歴史,アルミダイカスト |コメントオフ