インベストメント鋳造におけるラピッドプロトタイピング技術の応用
ラピッドプロトタイピング(RP)は、1990年代に開発されたハイテクです。 それは人々の心の中のデザインコンセプトをすぐに実際のオブジェクトに変えることができます。 特に、製品開発プロセス全体で金型やプロセス機器を必要としないため、試作品や新製品の試作サイクルが大幅に短縮され、企業の競争力を高めるための重要な手段やツールになります。 INCAST 2004が発行したインターネットアンケート調査(11)は、ヨーロッパの93を超えるインベストメント鋳造メーカーの400%以上がラピッドプロトタイピングを使用していることを示しています。 すべてのインタビュー対象者は、この新しいテクノロジーの使用が新製品を加速するために不可欠であることに同意します。 企業が市場に迅速に対応する能力を開発し、強化することは非常に重要です。
インベストメント鋳造における一般的なラピッドプロトタイピング法の適用
インベストメント鋳造におけるラピッドプロトタイピング技術の適用には、主に次の側面が含まれます。
1.投資する
ラピッドプロトタイピングマシンは、パターンを作成するときに、他のCADソフトウェアによって確立された12次元の幾何学的モデルを入力できるだけでなく、産業用CT(コンピューター断層撮影)によってスキャンされたデータファイルを受信することもできます。 たとえば、最初にパーツ(スクリュープロペラ、図1-12a)をCTでスキャンして、その断面の1次元画像を取得します(図12-1b)。 続いて、画像処理ソフトウェアは、各セクションの12次元画像(図1-12c)を組み合わせて、1次元の幾何学的モデル(図2-XNUMXd)を形成します。 次に、それをラピッドプロトタイピングマシンに送信してパターンを作成します(図XNUMX-XNUMXe)[XNUMX]。 この復元(リバース)エンジニアリング手法は、機械部品を復元できるだけでなく、特定の人間の臓器を模倣することもできます。
2.金型(圧縮成形)およびその他のプロセス機器の作成
ラピッドプロトタイピングによって精密鋳造金型を作成するには、2つの方法があります。XNUMXつは最初にマスター金型を作成し、次にエポキシまたはシリコーンゴムのプロファイリングを再作成する方法です。 もうXNUMXつの方法は、CADシステムで生成されたXNUMX次元プロファイリングブロックを使用することです。幾何学的モデルをラピッドプロトタイピングマシンに直接入力して、樹脂成形を行います。 このタイプのプロファイリングは、主に小ロット生産(数十個)に適しています。 マスターモールドの表面に厚さ約XNUMXmmの金属層を吹き付け、その後エポキシ樹脂を充填して金属-エポキシ複合プロファイルを作成すると、何百もの精密鋳造品を製造する要件を満たすことができます。 たとえば、SLS法を使用する場合、処理対象は樹脂粉末から表面に熱硬化性樹脂の薄層を備えた鋼粉末に変更され、レーザー焼結されてコンパクトになり、次に焼成されて樹脂が除去され、最後に銅液が除去されます。コンパクトの細孔に浸透します。 結果として得られるプロファイリングは、強度と熱伝導率の点で金属に似ています。 さらに、ラピッドプロトタイピング技術を使用して、特定の不規則な形状の金型を作成することもできます。
3.モールドキャスティングの直接生産
1990年代初頭、米国のサンディアナ国立研究所は、ダイレクトシェルキャスティング(DSPC)と名付けられたファストキャスティング(FastCAST)と呼ばれる特別な研究を実施しました。 残念ながら、後で報告されることはほとんどありません。
1994年、米国のZ Corporationは、3D印刷技術3DPrintingの開発に成功しました。 この技術は元々、マサチューセッツ工科大学のElySachs教授によって発明され特許を取得しました。 基本的な原理はSLS法に似ています。 最初に、耐火材料またはプラスチック粉末の層がローラーで噴霧されます。 SLSとの違いは、レーザー発光ヘッドを駆動する代わりに、インクジェットプリントヘッドを駆動して、製品の断面形状に応じて「印刷」用の接着剤をスプレーすることです。 パーツが完成するまで上記のアクションを繰り返し、「3Dプリントテクノロジー」と名付けました。 その利点は、低い運用コストと材料費、および高速です。 溶射粉末が石膏とセラミックの混合粉末の場合、アルミニウム、マグネシウム、亜鉛、およびZCastと呼ばれるその他の非鉄合金鋳物を鋳造するための型(石膏型)に直接かつ迅速に作ることができます(図12-2)。 。
一般的に使用されるラピッドプロトタイピング方法の比較アプリケーションの効果
現在、実際の生産でより一般的なラピッドプロトタイピング方法には、XNUMX次元リソグラフィー(SLA)、選択的レーザー焼結(SLS)、溶融堆積(FDM)、ラミネート製造(LOM)、直接モールドキャスティング(DSPC)などがあります。 近年、多くの外国の研究機関が、生産パターンの品質とインベストメント鋳造の性能の観点から上記の方法を比較しています。 結果は次のとおりです。
- 1)SLA法はパターンの寸法精度が最も高く、SLSとFDMがそれに続き、LOM法が最も低くなります[4]。
- 2)パターンの表面粗さパターンの表面を研磨して仕上げ、表面粗さ計で測定します。 結果を表12-1に示します[4]。 SLA法とLOM法では表面粗さが細かく、FDM法が最も厚いことがわかります。
- 3)微細部品の再現能力歯高約3mmのラックを対象として、これら4つの微細部品の再現能力を調べた。 その結果、SLAが最高で、FDMが最悪です[3]。
- 4)インベストメント鋳造の性能上記のXNUMXつの方法の中で、製品自体はワックスモールド法(FDMやSLSなど)であり、インベストメント鋳造プロセスの要件に簡単に適応でき、間違いなくパフォーマンスが向上します。 樹脂や型紙も焼くことができますが、ワックス型ほどインベストメント鋳造の要件に適応するのは簡単ではありません。 不利な点を回避するには、継続的な改善が必要です。
パターンの表面粗さの比較
測定部 | LOM | SLS | FDM | SLA |
レベルプレーン | 1.5 | 5.6 | 14.5 | 0.6 |
傾斜面 | 2.2 | 4.5 | 11.4 | 6.9 |
垂直面 | 1.7 | 8.2 | 9.5 | 4.6 |
全体的な観点から、SLA法はインベストメント鋳造プロセスとは多少の非互換性がありますが、その優れた寸法精度と表面品質のために人気があります。 海外、特に航空宇宙および軍事産業では、インベストメント鋳造企業が広く使用されています。 SLS法の品質はSLAの品質よりわずかに劣りますが、インベストメント鋳造のプロセス要件に簡単に適応できます。 したがって、ますます多くのアプリケーションが国内のインベストメント鋳造で使用されています。 FDM法はインベストメント鋳造のプロセス要件に適応するのが最も簡単ですが、ワックス型の寸法精度と表面品質は満足のいくものではありません。 LOM法は許容できる品質ですが、インベストメント鋳造に適応することは困難です。 したがって、インベストメント鋳造に適応することは困難です。 インベストメント鋳造におけるXNUMXつの方法の促進と適用には、一定の制限があります。
インベストメント鋳造におけるSLAおよびSLSの適用における新しい開発
1.新しい光硬化性樹脂
SLA法は、早くも1987年に商品化されました。元々は、特定の機能を備えた物理モデルやプロトタイプを作成するために使用されていました。 1990年代初頭、米国の3D System IncのQuickCastソフトウェアの開発に成功し、SLAラピッドプロトタイピングマシンで、滑らかで緻密な外観(図12)を維持しながらハニカム形状の構造(図3-12a)を作成できるようになりました。 -3b)、成形材料の90%を節約するだけでなく、シェルを焼成すると、パターンはシェルにひびが入ることなく最初に内側に崩壊します。 さらに、金型製造用の光硬化性樹脂については、次の特別な要件も満たす必要があることを人々は徐々に発見しました。
- 粘度-樹脂の粘度が高すぎると、パターンが作成された後、キャビティ内に残っている樹脂を排出することが困難になります。 残留樹脂が多すぎると、ベーキング中にシェルにひびが入る可能性があるため、遠心分離が必要になることがよくあります。 対策。 また、完成した模様の表面も掃除が難しいです。
- 残留灰-これはおそらく最も重要な要件です。 シェルを焼いた後の残留灰は、鋳造物の表面に非金属介在物やその他の欠陥を引き起こします。
- ・重金属元素の含有量-これは超合金の鋳造にとって特に重要です。 たとえば、アンチモンはSLA光硬化性樹脂で比較的一般的な元素です。 シェルが焼成された後に残留灰に現れると、合金を汚染し、鋳造物が廃棄される可能性さえあります。
- 寸法安定性-パターンのサイズは、操作全体を通して安定している必要があります。 このため、樹脂の吸湿性が低いことも非常に重要です。
近年、米国のDSM Somosは、上記の主な要件を満たし、インベストメント鋳造メーカーに非常に好まれている新しいタイプの光硬化性樹脂Somos10120の開発に成功しました。 この新製品は、XNUMXつの異なる精密鋳造工場でXNUMXつの合金(アルミニウム、チタン、コバルト-モリブデン合金)で鋳造され、満足のいく結果を達成しました。
2.少量生産にはSLAモデルを使用します
SLAパターンを使用した精密鋳造の小ロット生産で考慮すべき11120つの主要な問題があります。50つはパターンと鋳造が達成できる寸法精度であり、もう95つは製造コストと納期に利点があるかどうかです。 Solidiform、Nu-Cast、PCC、Uni-Castなど、米国のいくつかの精密鋳造工場では、SLAパターンを使用して何百もの鋳造品を鋳造しています。 鋳造サイズを実際に測定した後、統計分析により、DSMSomosによって開発された新しい12光硬化樹脂が使用されていることが示されています。 QuickCastテクノロジーを使用すると、結果のSLAパターンのサイズ偏差は鋳造公差値の4%以下になります。 ほとんどの鋳物のサイズは公差要件を満たし、合格率は7%を超えています(図XNUMX-XNUMX)[XNUMX]。
SLAパターンを作成するコストは、同じワックスモールドを作成するコストよりもはるかに高く、時間がかかりますが、プロファイリングを設計および製造する必要はありません。 したがって、単一のピースが小さなバッチで生産される場合でも、コストと納期は利点です。 鋳造が複雑になるほど、この利点はより明白になります。 Nu-Castが製造した複雑な形状の航空精密鋳造を例にとると(図12-5)[7]、金型製作コストは約85,000米ドルで、毎日4つのワックス金型が生産され、各ワックスのコストがかかります。カビ(材料と労働力を含む)150米ドル。 SLA法を採用した場合、各SLAモデルのコストは2846米ドルですが、金型を設計および製造する必要はありません。 この計算から、出力が32個未満の場合、SLA金型を使用するコストはワックス金型よりも低くなります。 32個を超える場合、コストはワックス型よりも高くなります(図12-6)。 ワックス金型を使用すると、金型の設計と製造に14〜16週間かかります。また、SLA金型は金型を必要としません。 したがって、SLA金型を使用して、出力が87個未満の場合、鋳造品の配送はワックス金型よりも速くなります(図12-7)。 しかし、87個以上の場合、ワックスモールドの方が高速です[7]。 考慮しなければならないもうXNUMXつの要素は、ワックスモールドを使用する場合、製品を更新するときにモールドを作り直す必要があることです。これにはコストがかかります。 SLAの外観では、CADジオメトリモデルを変更するだけで済みます。これは、金型を作り直すよりもはるかに簡単で高速です。 。
3.SLS焼結ポリスチレン粉末含浸ワックスパターン
SLSは当初、レーザーを使用して特殊なワックス粉末をワックス型に焼結しました。これは、インベストメント鋳造のプロセス特性に非常に適しています。 1990年の終わりには、米国に50以上の鋳造所があり、約3000のワックス型を製造し、鋳造に成功しました。 さまざまな金属鋳物を製造します。 ただし、ワックスパウダーは最も理想的な成形材料ではありません。 それから作られたワックス型の強度が不十分であり、温度が高いと軟化および変形しやすく、温度が低いと壊れやすい。 そのため、1990年代初頭、米国の一部のSLAユーザーは、ワックス粉末をポリスチレン(PS)やポリカーボネート(PC)などの熱可塑性粉末に置き換えようとしました。 この種の材料は、ルーズで多孔質の形状(気孔率が25%以上)になっているため、離型時にシェルが膨潤したり割れたりするリスクが軽減されます。 シェルが焼成された後、灰の含有量は少なくなりますが、パターンの表面は粗くなります。 したがって、パターンを作成した後、表面を滑らかで緻密にするために、手作業でワックスを塗って磨く必要があります。 現在、この方法は国内外で広く利用されています。
転載のためにこの記事の出典と住所を保管してください:インベストメント鋳造におけるラピッドプロトタイピング技術の応用
Minghe Casting Companyは、高品質で高性能な鋳造部品の製造と提供に専念しています(金属ダイカスト部品の範囲には主に次のものが含まれます) 薄肉ダイカスト,ホットチャンバーダイカスト,コールドチャンバーダイカスト)、ラウンドサービス(ダイカストサービス、CNCの機械化,金型製作、表面処理)。カスタムのアルミニウムダイカスト、マグネシウムまたはザマック/亜鉛ダイカスト、およびその他の鋳造要件については、お問い合わせください。
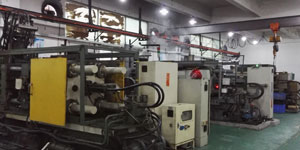
ISO9001とTS16949の管理下で、すべてのプロセスは、ブラスターからウルトラソニック洗濯機に至るまで、何百もの高度なダイキャスティングマシン、5軸マシン、およびその他の設備を介して実行されます。経験豊富なエンジニア、オペレーター、検査官のチームがお客様の設計を実現します。
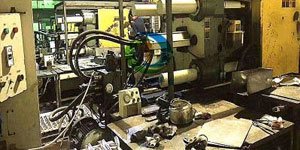
ダイカストの委託製造業者。 機能には、0.15ポンドからのコールドチャンバーアルミニウムダイカスト部品が含まれます。 6ポンドまで、クイックチェンジセットアップ、および機械加工。 付加価値サービスには、研磨、振動、バリ取り、ショットブラスト、塗装、メッキ、コーティング、組み立て、および工具が含まれます。 使用する材料には、360、380、383、413などの合金が含まれます。
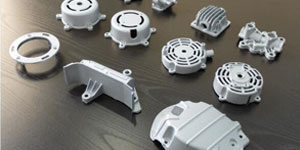
亜鉛ダイカスト設計支援/コンカレントエンジニアリングサービス。 精密亜鉛ダイカストのカスタムメーカー。 ミニチュア鋳造、高圧ダイカスト、マルチスライドモールド鋳造、従来のモールド鋳造、ユニットダイおよび独立ダイカスト、およびキャビティシール鋳造を製造することができます。 鋳物は、最大24インチインチ+/- 0.0005インチの公差で長さと幅で製造できます。
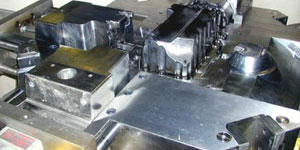
ISO 9001:2015年にダイキャストマグネシウムの認定メーカー。機能には、最大200トンのホットチャンバーと3000トンのコールドチャンバーの高圧マグネシウムダイカスト、工具設計、研磨、成形、機械加工、粉末および液体塗装、CMM機能を備えたフルQAが含まれます。 、組み立て、梱包、配送。
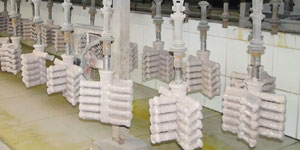
ITAF16949認定済み。 追加の鋳造サービスが含まれます インベストメント鋳造,砂型鋳造,重力鋳造, ロストフォームキャスティング,遠心鋳造,真空鋳造,永久鋳型鋳造、。機能には、EDI、エンジニアリング支援、ソリッドモデリング、および二次処理が含まれます。
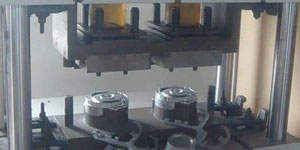
鋳造業 部品のケーススタディ:車、バイク、航空機、楽器、船舶、光学機器、センサー、モデル、電子機器、エンクロージャー、時計、機械、エンジン、家具、ジュエリー、ジグ、テレコム、照明、医療機器、写真機器、ロボット、彫刻、音響機器、スポーツ機器、工具、おもちゃなど。
次に何ができるでしょうか?
∇ホームページに移動 ダイカスト中国
By ミンゲダイカストメーカー |カテゴリ: 役立つ記事 |材料 タグ: アルミ鋳造, 亜鉛鋳造, マグネシウム鋳造, チタン鋳造, ステンレス鋼鋳造, 真ちゅう鋳造,ブロンズ鋳造,キャスティングビデオ,会社の歴史,アルミダイカスト |コメントオフ