粉末冶金(P / M)部品の切削加工
自動車用動力システムの部品を製造するための粉末冶金(P / M)プロセスの使用は増え続けています。 P / Mプロセスで製造された部品には、多くの重要でユニークな利点があります。 これらの部品に意図的に残された残留多孔質構造は、自己潤滑と遮音に適しています。 従来の鋳造プロセスでは製造が困難または不可能な複雑な合金は、P / M技術を使用して製造できます。 この技術で製造された部品は、通常、処理能力がほとんどまたはまったくないため、安価で材料の無駄が少なくなります。 残念ながら、これらの機能の魅力の背後には、P / M部品の加工が困難です。
P / M業界の本来の意図のXNUMXつはすべての処理を排除することですが、この目標はまだ達成されていません。 ほとんどの部品は「最終形状に近い」だけであり、それでもある程度の仕上げが必要です。
ただし、鋳物や鍛造品と比較して、P / M部品から除去する必要のある少量の材料が典型的な耐摩耗性材料です。
多孔質構造は、p / M部品の用途が広い特徴の20つですが、多孔質構造によって工具寿命も損なわれます。 多孔質構造は油と音を蓄えることができますが、それはまた微小な断続的な切断につながります。 穴から固体粒子に前後に移動するとき、ツールチップは継続的に衝撃を受けます。これにより、非常に小さな疲労破壊変形と、刃先に沿った微細なエッジの崩壊が発生する可能性があります。 さらに悪いことに、粒子は通常非常に硬いです。 測定された材料のマクロ硬度が35〜60度であっても、コンポーネントの粒子サイズはXNUMX度にもなります。 これらの硬い粒子は、深刻で急速なエッジ摩耗を引き起こします。 多くのp / M部品は熱処理可能であり、材料の硬度と強度は熱処理後に高くなります。 最後に、焼結および熱処理技術と使用されるガスにより、材料の表面には、硬くて耐摩耗性のある酸化物および/または炭化物が含まれます。
P / Mパーツの性能
被削性を含むP / M部品のほとんどの特性は、合金の化学組成だけでなく、多孔質構造の気孔率レベルにも関係しています。 多くの構造部品の気孔率は最大15%〜20%です。 ろ過装置として使用される部品の気孔率は50%にもなることがあります。 シリーズのもう一方の端では、鍛造またはヒップパーツの気孔率はわずか1%以下です。 これらの材料は、より高いレベルの強度を達成できるため、自動車および航空機の用途で特に重要になっています。
P / M合金の引張強度、靭性、延性は密度の増加とともに増加し、気孔率は工具先端に有害であるため、被削性も向上する可能性があります。
気孔率の増加は、部品の遮音性能を向上させることができます。 標準部品の減衰振動は、P / M部品で大幅に低減されます。これは、工作機械、空調ブローパイプ、および空気圧工具にとって非常に重要です。 自己潤滑歯車にも高い気孔率が必要です。
機械加工の難しさ
P / M産業の継続的な発展の目標のXNUMXつは機械加工を排除することであり、P / Mプロセスの主な魅力のXNUMXつは少量の処理しか必要としないことですが、多くの部品はまだ後処理が必要です。より高い精度またはより良い表面仕上げ。 残念ながら、これらの部品の機械加工は非常に困難です。 発生する問題のほとんどは、多孔性が原因です。 気孔率は、刃先の微小疲労につながります。 最先端は絶えず切り込みと切り出しを行っています。 粒子と穴の間を通過します。 小さな衝撃を繰り返すと、刃先に小さな亀裂が生じます。
これらの疲労亀裂は、刃先が崩壊するまで成長します。 この種のマイクロチッピングエッジは通常非常に小さく、通常は通常のアブレシブ摩耗を示します。
気孔率はまた、P / M部品の熱伝導率を低下させ、その結果、刃先が高温になり、クレーターの摩耗や変形が発生します。 内部で接続された多孔質構造は、切削領域から切削液を排出するための経路を提供します。 これは、特に掘削時に、高温の亀裂や変形を引き起こす可能性があります。
内部の多孔質構造によって引き起こされる表面積の増加は、熱処理中の酸化および/または炭化にもつながります。 前述のように、これらの酸化物と炭化物は硬く、耐摩耗性があります。
多孔質構造はまた、非常に重要な部品の硬度の読み取りの失敗をもたらします。 P / M部品のマクロ硬度を意図的に測定する場合、穴の硬度の要素が含まれます。 多孔質構造は構造の崩壊につながり、比較的柔らかい部品の誤った印象を与えます。 粒子ははるかに硬いです。 上記のように、違いは劇的です。
PM部品に介在物が存在することも不利です。 加工時にこれらの粒子が表面から引き上げられ、工具の前でこすったときに部品の表面に引っかき傷または引っかき傷が形成されます。 これらの介在物は通常大きく、部品の表面に目に見える穴を残します。
炭素含有量の違いは、被削性の不一致につながります。 たとえば、fc0208合金の炭素含有量は0.6%から0.9%の範囲です。 炭素含有量が0.9%の材料のバッチは比較的硬く、工具寿命が短くなります。 炭素含有量が0.6%の材料の他のバッチは、優れた工具寿命を備えています。 どちらの合金も許容範囲内です。
最終的な機械加工の問題は、P / M部品で発生する切削のタイプに関連しています。 部品が最終形状に近いため、通常、切削深さは非常に浅くなります。 これには、自由な刃先が必要です。 刃先に切りくずがたまると、マイクロチッピングが発生することがよくあります。
処理技術
これらの問題を克服するために、いくつかの技術(業界独自)が適用されています。 表面の多孔質構造は、浸透によって密封されることがよくあります。 通常、追加のフリーカットが必要です。 最近、熱処理中の粉末の清浄度を高め、酸化物および炭化物を低減するように設計された改良された粉末製造技術が使用されてきた。
閉じた表面の多孔質構造は、金属(通常は銅)またはポリマーの浸透によって実現されます。 浸透は潤滑剤として作用すると推測されています。 実験データのほとんどは、真の利点は表面の多孔質構造を閉じて、刃先の微小疲労を防ぐことにあることを示しています。 びびりの低減により、工具寿命と表面仕上げが向上します。 浸透の最も劇的な使用は、多孔質構造が閉じているときに工具寿命が200%増加することを示しています。
MNS、s、MoS2、MgSiO3、BNなどの添加剤は工具寿命を延ばすことが知られています。 これらの添加剤は、切りくずがワークピースから分離しやすくなり、切りくずを破壊し、切りくずの蓄積を防ぎ、刃先を潤滑することにより、被削性を向上させます。 添加剤の量を増やすと、被削性は向上しますが、強度と靭性は低下します。
焼結および熱処理炉ガスを制御する粉末噴霧技術により、清浄な粉末および部品を製造することが可能になり、介在物および表面酸化物炭化物の発生が最小限に抑えられます。
ツール素材
P / M業界で最も広く使用されている工具は、良好な表面仕上げの条件下で、耐摩耗性、耐エッジクラック性、および切りくずのない材料です。 これらの特性は、あらゆる機械加工操作、特にP / M部品に役立ちます。 このカテゴリに含まれる工具材料は、立方晶窒化ホウ素(CBN)工具、コーティングされていないサーメットとコーティングされたサーメット、および改良されたコーティングされた焼結超硬合金です。
CBNツールは、硬度と耐摩耗性が高いため魅力的です。 この工具は、ロックウェル硬度45以上の鋼および鋳鉄の加工に長年使用されてきました。 ただし、P / M合金の独自の特性と、ミクロ硬度とマクロ硬度の大きな違いにより、ロックウェル硬度が25のP / M部品にはCBNツールを使用できます。重要なパラメータは粒子の硬度です。 粒子の硬度がロックウェル50度を超える場合、マクロ硬度値に関係なくCBNツールを使用できます。 これらのツールの明らかな制限は、それらの靭性の欠如です。 断続切削や高気孔率の場合は、ネガティブ面取りやヘビーホーニングなどのエッジ補強が必要です。 研ぎ澄まされた刃先で簡単な軽切削が可能です。
効果的なCBNの材料はいくつかあります。 最高の靭性を備えた材料は、主にCBN全体で構成されています。 靭性に優れているため、荒加工に使用できます。 それらの制限は通常、表面仕上げに関連しています。 これは主に、ツールを構成する個々のCBN粒子によって決定されます。 粒子が刃先から落下すると、被削材の表面に影響を与えます。 ただし、微粒子ツールがXNUMXつのパーティクルから落ちるほど深刻ではありません。
通常使用されるCBN材料は、CBNの含有量が高く、粒子サイズが中程度です。 CBN仕上げ刃は細粒で、CBN含有量が少ない。 軽い切削や表面仕上げが必要な場合や、加工する合金が特に硬い場合に最も効果的です。
多くの切削用途では、工具寿命は材料の種類に依存しません。 言い換えれば、どのCBN材料でも同様の工具寿命を達成できます。 これらの場合、材料の選択は主に各刃先の最低コストに基づいています。 XNUMXつの丸いブレードはCBN上面全体を持ち、XNUMXつ以上の刃先を提供できます。これはXNUMXつの象眼細工のCBNブレードよりも安価です。
P / M部品の硬度がロックウェル35度より低く、粒子の硬度が範囲内にある場合、通常、サーメットが選択肢のXNUMXつです。 サーメットは非常に硬く、チップの蓄積を効果的に防ぎ、高速に耐えることができます。 さらに、サーメットは常に鋼やステンレス鋼の高速および仕上げ加工に使用されてきたため、通常、成形部品の近くに適した理想的な幾何学的な溝があります。
今日のサーメットは、最大11の合金元素を使用して、冶金学が複雑になっています。 それらは通常、TiCN粒子とNiMo接着剤から焼結されます。 TiCNは、サーメットの使用を成功させるために重要な硬度、切りくずの蓄積耐性、および化学的安定性を提供します。 さらに、これらのツールは通常、接着剤の含有量が高いため、靭性が良好です。 一言で言えば、それらはP / M合金を効果的に処理するすべての特徴を持っています。 炭化タングステン焼結超硬合金と同様に、いくつかの種類のサーメットが効果的であり、バインダーの含有量が多いほど、靭性が向上します。
既知の比較的新しい開発は、中温化学蒸着(mtcvd)もP / M業界に利点を提供することです。 Mtcvdは、従来の化学蒸着(CVD)のすべての耐摩耗性とクレーター耐摩耗性を保持しますが、靭性を客観的に向上させます。 靭性の増加は、主に亀裂の減少によるものです。 コーティングは高温で堆積され、炉内で冷却されます。 一貫性のない熱膨張によりツールが室温に達すると、コーティングに亀裂が含まれます。 板ガラスの傷と同様に、これらの亀裂は刃先の強度を低下させます。 mtcvdのより低い堆積温度は、より低い亀裂頻度とより良い刃先の靭性につながります。
CVDコーティングとmtcvdコーティングの基板が同じ特性とエッジドレッシングを持っている場合、それらの靭性の違いを示すことができます。 エッジ靭性が要求される用途で使用する場合、mtcvdコーティングの性能はCVDコーティングの性能よりも優れています。 分析により、多孔質構造のP / M部品を加工する場合、エッジの靭性が重要になります。 MtcvdコーティングはCVDコーティングよりも優れています。
物理蒸着(PVD)コーティングは、mtcvdまたはCVDコーティングよりも薄く、耐摩耗性が低くなっています。 ただし、PVDコーティングはアプリケーションでの大きな影響に耐えることができます。 PVDコーティングは、切削が摩耗、CBNおよびサーメットが脆すぎて、優れた表面仕上げが必要な場合に効果的です。
たとえば、C-2超硬合金の刃先は、0205 m / minの線速度と180mm /回転の送り速度でfc0.15に加工できます。 20個の部品を加工した後、切りくずの蓄積により微小崩壊が発生する可能性があります。 PVD窒化チタン(TIN)コーティングを使用すると、切りくずの蓄積が抑制され、工具寿命が延びます。 この試験にスズコーティングを使用した場合、P / M部品のアブレシブ摩耗特性はTiCNコーティングでより効果的であると予想されます。 TiCNは、スズとほぼ同じ耐チップ蓄積性を備えていますが、スズよりも硬く、耐摩耗性に優れています。
多孔質構造は重要であり、fc0208合金の被削性に影響を与えます。 多孔質の構造と特性が変化すると、さまざまな工具材料が対応する利点を提供します。 密度が低い場合(6.4g / cm3)、マクロ硬度は低くなります。 この場合、mtcvdでコーティングされた超硬合金が最高の工具寿命を提供します。 刃先の微小疲労は非常に重要であり、刃先の靭性は非常に重要です。 この場合、優れた靭性のサーメットブレードが最大の工具寿命を提供します。
密度6.8g / cm3の同じ合金を製造する場合、エッジクラックよりもアブレシブ摩耗が重要になります。 この場合、mtcvdコーティングは最高の工具寿命を提供します。 PVDコーティングされた超硬合金は、XNUMX種類の非常に硬い部品のテストに使用され、刃先に触れると破損します。
速度が上がると(線速度が毎分300メートルを超える)、サーメットやコーティングされたサーメットでさえクレーターの摩耗が発生します。 特にコーティングされた超硬合金の刃先靭性が良好な場合は、コーティングされた超硬合金がより適しています。 Mtcvdコーティングは、コバルトが豊富な領域を持つ超硬合金に特に効果的です。
サーメットは、旋削やボーリングで最も一般的に使用されます。 PVDコーティングされた超硬合金は、低速での堆積への注意が期待されるため、ねじ加工に最適です。
転載のためにこの記事の出典と住所を保管してください:粉末冶金(P / M)部品の切削加工
Minghe Casting Companyは、高品質で高性能な鋳造部品の製造と提供に専念しています(金属ダイカスト部品の範囲には主に次のものが含まれます) 薄肉ダイカスト,ホットチャンバーダイカスト,コールドチャンバーダイカスト)、ラウンドサービス(ダイカストサービス、CNCの機械化,金型製作、表面処理)。カスタムのアルミニウムダイカスト、マグネシウムまたはザマック/亜鉛ダイカスト、およびその他の鋳造要件については、お問い合わせください。
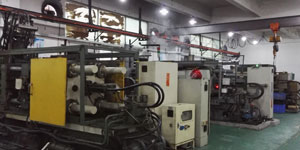
ISO9001とTS16949の管理下で、すべてのプロセスは、ブラスターからウルトラソニック洗濯機に至るまで、何百もの高度なダイキャスティングマシン、5軸マシン、およびその他の設備を介して実行されます。経験豊富なエンジニア、オペレーター、検査官のチームがお客様の設計を実現します。
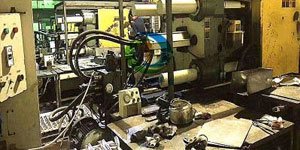
ダイカストの委託製造業者。 機能には、0.15ポンドからのコールドチャンバーアルミニウムダイカスト部品が含まれます。 6ポンドまで、クイックチェンジセットアップ、および機械加工。 付加価値サービスには、研磨、振動、バリ取り、ショットブラスト、塗装、メッキ、コーティング、組み立て、および工具が含まれます。 使用する材料には、360、380、383、413などの合金が含まれます。
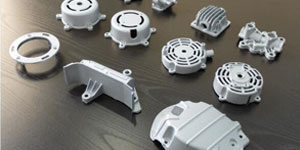
亜鉛ダイカスト設計支援/コンカレントエンジニアリングサービス。 精密亜鉛ダイカストのカスタムメーカー。 ミニチュア鋳造、高圧ダイカスト、マルチスライドモールド鋳造、従来のモールド鋳造、ユニットダイおよび独立ダイカスト、およびキャビティシール鋳造を製造することができます。 鋳物は、最大24インチインチ+/- 0.0005インチの公差で長さと幅で製造できます。
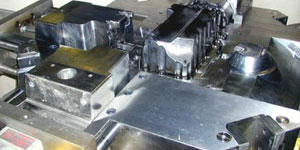
ISO 9001:2015年にダイキャストマグネシウムの認定メーカー。機能には、最大200トンのホットチャンバーと3000トンのコールドチャンバーの高圧マグネシウムダイカスト、工具設計、研磨、成形、機械加工、粉末および液体塗装、CMM機能を備えたフルQAが含まれます。 、組み立て、梱包、配送。
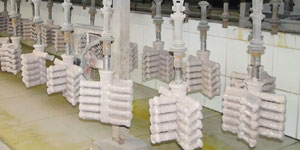
ITAF16949認定済み。 追加の鋳造サービスが含まれます インベストメント鋳造,砂型鋳造,重力鋳造, ロストフォームキャスティング,遠心鋳造,真空鋳造,永久鋳型鋳造、。機能には、EDI、エンジニアリング支援、ソリッドモデリング、および二次処理が含まれます。
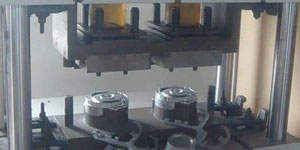
鋳造業 部品のケーススタディ:車、バイク、航空機、楽器、船舶、光学機器、センサー、モデル、電子機器、エンクロージャー、時計、機械、エンジン、家具、ジュエリー、ジグ、テレコム、照明、医療機器、写真機器、ロボット、彫刻、音響機器、スポーツ機器、工具、おもちゃなど。
次に何ができるでしょうか?
∇ホームページに移動 ダイカスト中国
By ミンゲダイカストメーカー |カテゴリ: 役立つ記事 |材料 タグ: アルミ鋳造, 亜鉛鋳造, マグネシウム鋳造, チタン鋳造, ステンレス鋼鋳造, 真ちゅう鋳造,ブロンズ鋳造,キャスティングビデオ,会社の歴史,アルミダイカスト |コメントオフ