不十分な球状化の17の理由と制御
1960年代と1970年代には、コークスの品質が低いため(塊が大きく、密度が低く、固定炭素含有量が少なく、硫黄含有量が少ない)、キューポラは主にダクタイル鋳鉄の製造に使用されていました。 溶銑の低温; 使用する結節剤の調製方法は完全ではありません。 銑鉄は硫黄分とリン分を多く含んでいるため、ダクタイル鋳鉄の品質が悪く、球状化の品質が不安定です。 現在、ダクタイル鋳鉄の製造は主に電気炉で製錬されており、炉の温度は簡単に制御できます。 銑鉄などの原材料の品質は良好です。 ダクタイル鋳鉄には多くの種類があり、品質が良いので、ダクタイル鋳鉄の品質を管理しやすくなっています。 ただし、ダクタイル鋳鉄の製造における主な欠陥のXNUMXつは、球状化の不良です。
不十分な球状化は、大きな黒い斑点または明らかな小さな黒い斑点を伴う、鋳造物の破壊(通常、注入ライザーの破壊を観察します)に現れます。 キャスティングを打つ音ははっきりと鮮明ではありません。 金属組織の微細構造には多くの厚い部分があります;少量の回転楕円体グラファイト、凝集グラファイト、または樹枝状グラファイトがあります(球状化が不十分な場合、金属組織学的特徴があります。つまり、厚いフレークグラファイトクラスターでは、個々の回転楕円体グラファイトはかなり丸みを帯びています) 。
球状化不良の原因は、一般に次のXNUMX種類の要因の影響を受けます。残留マグネシウム含有量または希土類含有量が低すぎる(ただし、希土類含有量が高すぎると、黒鉛の丸みが悪くなり、鋳造が起こりやすくなります。白い口に。そして縮む松); 接種効果は強くも低下もしていません。 干渉要素が高すぎます。
しかし、実際の製造工程では、技術的な問題、運用上の問題、管理上の問題など、球状化が不十分になる多くの要因があります。
1.球状化剤の品質が悪い
球状化剤中のMgとREの含有量は、実験室試験による品質要件を満たしていますが、製錬技術が不十分なため、MgO含有量は比較的高くなっています(球状化剤にはMgO> 1%が含まれているため、球状化の品質に影響を与える可能性があります)。 MgOは改善できます球状化の品質はほとんど効果がありませんが、ダクタイル鋳鉄はスラグ含有欠陥を起こしやすいです。 球状化剤はCaなどの元素が少なく、球状化処理中の反応は激しく、Mgはより多く燃焼します。
予防策:低品質のノジュライザーを使用しないでください(サプライヤーとメーカーを検査し、最初に少量を購入し、試用後にまとめて購入する必要があります)。 球状化剤の配置が長すぎると、湿気や酸化が起こりやすくなります。
2.炉前での球状化の不適切な操作
球状化剤は溶鉄取鍋ダムのピットに流し込まれ、平坦化されません。 表面被覆が小さいか、被覆層が薄いか、球状化剤ブロックの隙間が埋められていない。 溶銑に突入した後、球状化が露出するだけでなく、薬剤がすぐに溶けて反応すると同時に、大量の溶融鉄が球状化剤ブロックの隙間に入り、球状化剤を直接溶融するか、球状化物を洗浄する浮遊溶銑の表面から薬剤が離れると、反応が早すぎて速すぎて、Mgがさらに燃焼します。
予防策:バッグの底にあるピットに注がれた球状化剤を平らにして適切に叩き、次にその上に覆われた接種済みフェロシリコンを平らにして叩き、適切な量の結節性鋳鉄ファイリング(叩き)またはダクタイル鋳鉄で表面を覆います特定の厚さのプレート。 これは合金の隙間を埋めるだけでなく、一定の厚さの被覆層も持っています。
3.元の溶鉄は硫黄含有量が高い
硫黄は主な脱球状化元素であり、硫黄含有量が高いと球状化の品質に深刻な影響を及ぼします。 元の溶銑のwSが0.06%を超えると、球状化剤を追加しても、適格な球状黒鉛鋳鉄の品質を得ることが困難になります。 。 球状化プロセス中、球状化剤中のMgは最初に溶鉄中のSと化学的に反応してMgSのスラグを形成し、残りのMgは球状化の役割を果たします。これはREにも当てはまります。 球状化要素が少ないため、球状化の品質に影響します。 溶銑は硫黄分が多い。 球状化剤を大量に添加しても、注入時間が長すぎてスラグがきれいでない場合、「硫黄の戻り」現象が発生し、注入から後期までの鋳物の品質に影響を及ぼします。 。 元の溶銑に含まれる硫黄の主な発生源は、硫黄含有量の高いコークスまたは新生鉄の使用です。
予防策:低硫黄銑鉄を使用し、材料とコークスをリサイクルします。 添加されたノジュライザーの量と元の溶鉄の硫黄含有量との関係を把握します。 炉の前と球形化プロセス中に脱硫対策を講じる(コークスに石灰を噴霧する)水と電気炉で脱硫し、球形化バッグにアルカリ表面または苛性ソーダを追加する方が簡単です)
Ti、Sb、As、Pb、Al、Snなど、電荷で置換された球状化干渉元素は高すぎます。希土類元素には、球状化防止干渉元素を弱めたり相殺したりする特定の能力がありますが、干渉元素が多すぎます。溶鉄では、グラファイトの小塊(変形したグラファイト)の形状が劣化します。 球状化しても、ダクタイル鋳鉄の物性も非常に脆くなる傾向があります。 したがって、QT400-18および耐低温ダクタイル鋳鉄の製造では、高純度の銑鉄を使用する必要があります。
4.溶鉄取鍋の不適切な配置
鉄を叩くと、溶銑はピットに押し込まれた球状化剤に直接突入し、被覆を洗い流すだけでなく、合金ブロックを高温溶銑の衝撃に直接さらしたり、早期に溶けたりします。激しく反応する、または鉄に素早く浮く溶銑の表面が溶けて溶銑の表面で燃焼し、空気に吸収されるため、溶銑のMgへの吸収率が低下します。
予防策:溶銑が合金に直接衝突しないように溶銑取鍋を置き、溶銑が着実かつ迅速に合金を沈め、瞬時に一定の深さに達するようにし、合金が浮く距離を延ばして合金を作る溶鉄に完全に吸収されます。
5.スローアイアンタッピングが始まります
最初のアイロンタッピングが遅すぎると、取鍋内の液面がゆっくりと上昇します。 溶鉄が合金に溢れると、合金の表層が溶け始め、その後上昇します。 合金の表面と溶銑の表面との距離が短いため、合金には時間がありません。溶銑の表面に大量の溶銑が浮かんでいます。 溶銑表面でのMgの溶融・燃焼は空気に吸収されて失われ、Mgへの溶銑の吸収率が低下します。
予防策:キューポラ炉の場合、前炉床に十分な溶銑がなければなりません。 タップする前に、タップ穴をふさいでいる泥を取り除き、タップ穴をすばやく開いて、溶銑がすぐに届くようにします。 溶銑鍋容量の深さの2/3(すなわち、特定の深さ)。 このとき、球状化反応は、合金の表面から液面までの距離が大きいためです。 合金が溶銑に浮くと、移動距離が長くなり、浮くと同時に溶ける。 、エッジは溶銑に完全に吸収され、球状化剤中の球状化元素Mgは吸収率が高く、球状黒鉛鋳鉄の品質は良好です。 電気炉タッピングの方が便利です。反応が激しい場合は、すばやくタッピングを開始し、ゆっくりタッピングするか、タッピングを停止し、反応が安定している場合は、必要な量までタッピングを続けます。 応答が安定している場合は、できるだけ速くしてから遅くするようにしてください(途中でノンストップ)。XNUMX回のタイムアウト。
6.球状化剤の設置が早すぎるか、ダムのピット内の溶鉄が完全に注がれていない
注いだ後、赤いホットレードルの底の温度は900°Cより高くなります。 すぐに球状化剤を塗布すると、高温ベーキングでMgとREの一部が失われます(煙現象)。 堤防ピット内の溶鉄を洗浄しないと、Mgの損失が大きくなります。 さらに、過熱された予熱温度はまた、球状化剤の早期溶融を促進するであろう。
予防策:取鍋を一定時間冷まし、溶鉄を叩く前に球状化剤を充填します。 同時に、取鍋内に残っている溶銑を注いだ後、時間内に流し出し、取鍋内の溶融スラグを除去します。
7.球状化溶融鉄の温度が低すぎる
球状化溶融鉄の温度が1390℃を下回ると、合金が溶けにくくなり、球状化反応が不完全になり、球状化レベルが要件を満たすことが困難になります。 球状化剤の浮遊過程では、溶銑の温度が低いため、球状化剤がすぐに溶けて吸収されず、球状化剤が溶融鉄の表面に浮いて溶けて燃焼する。
8.球状化溶融鉄の温度が高すぎる
球状化液鉄の温度が高すぎ、被覆剤と球状化剤の溶融速度が速すぎる。 純粋なMgの密度は1.74g / cm3であるため、融点は651°C、沸点は1105°Cです。 融点は1400℃未満であり、球状化温度は1490〜1520℃であることが多く、それより高い場合もあります。 鋳物の大きさや壁の厚さに応じて、球形化温度を実際に上げる必要がある場合は、比較的「低温処理と高温鋳物」の対策を講じる必要があります。 また、溶銑の温度が高すぎると、溶銑が激しく酸化されることがよくあります。 MgとREは酸化物と反応しやすいため、高温ではMgとREの損失と蒸発が大きくなり、吸収率が低下します。
9.球状化剤は、小さな塊とより多くの破片を持っています
球状化剤のサイズが小さく、ピースが多い場合、球状化処理方法は同じですが、合金ブロック間に隙間がないため、溶融反応はゆっくりと層ごとに剥がすことができます。 同じ手順で注ぐと、最初の数箱の球形化がうまくいかず、最後の数箱の球形化がまだ良い場合があります。
予防策:溶銑取鍋の大きさ、つまり溶銑の球形化量に基づいて球形化剤の大きさを選択します。 破砕が多すぎる場合は、ふるいにかける必要があります。 球状化反応が遅すぎる場合は、スチールドリルを使用して、ロードされた合金を溶融鉄を通して数回粉砕し、溶融鉄を合金にドリルして球状化反応を加速することができます。
10.球状化剤が大きすぎる
球状化剤が大きすぎます。 浮いて溶ける過程で、溶銑に吸収されるのではなく、溶銑の表面に浮いて溶けて燃え、空気中に無駄になります。
球状化剤のブロックサイズの選択は、溶銑取鍋のサイズ、すなわち、結節状の溶銑の量に応じて決定されます。
11.少量の球状化剤を添加
添加される球状化剤の量は、材料の要件、溶銑の硫黄含有量、溶銑の品質、球状化温度、鋳物のサイズ、およびその他の要因に関連しています。 球状化剤が少ない理由はXNUMXつあります。XNUMXつは設計要件自体が小さいことです。 もうXNUMXつは、溶銑の量が十分に管理されておらず、溶銑の量が要件を超えていることです。
12.鉄液の酸化
酸化後の溶銑の酸素含有量は高い。 OとMgの間の強い親和性により、球状化剤中の有効な球状化元素Mgは最初にOと結合してMgOスラグを生成し、残りのMgはグラファイトを球状化することができます。 機能は、酸素が大量のMgを消費し、残りのMgがグラファイトを球形にするのに十分ではないため、球状化レベルが低く、球状化の品質が悪いためです。
予防策:溶鉄が酸化するのを防ぐために、キューポラのコークス(チャー)の高さが低いことに注意してください。 電気炉の溶解では、特に10t炉で溶融鉄を溶解する場合は、溶融鉄の過度の高温や高温での長期保存を防ぐために、過度に酸化された装入物を使用しないでください。 球状化工程が1tになるたびに、球状化工程が数パック後になると、炉内での溶銑の滞留時間が長いため、溶銑は「結晶核」を欠くだけでなく、酸化しやすい。 球状化処理後数パケットの場合は、まず炉内で「前処理」を行い、脱酸処理に適した量の炭化ケイ素、脱酸剤、再炭化剤、フェロシリコンなどを加え、適切に球状化剤を加えます。
13.バッグとバッグピットの深さ対直径の比率
- (1)球形化パッケージの深さHと直接Dの比率は、H / D = 1.5〜2です。 球状化バッグを使用してハーフバッグを処理すると、高い経済比率という当初の意図に反します。
- (2)球状化剤と被覆剤を充填した後、球状化バッグのピットの深さは20〜30mmである必要があります。 溶鉄がピットに入り、被覆剤が溶けて半固体になり、球状化剤の早期発生を遅らせます。 Mgの収量を向上させることができます。
- (3)鞄の底の穴の幅は、鞄の底の直径の1 / 4〜1 / 3でなければなりません。 投影面積が小さいピットは深さを増し、発生を遅らせるのに役立ちます。
- (4)スフェロイド化剤の各バッグが同じ方法でピットにロードされるように、注入後の時間内にバッグ内のスラグをクリーンアップします。
14.長い注入時間およびその他の理由による球状化の低下
球状化後退の特徴は次のとおりです。炉の前では良好な球状化が見られますが、鋳造では良好な球状化は見られません。 または同じ溶鉄の取鍋では、最初に注がれる鋳物は良好な球状化を示し、後で注がれる鋳物は十分に球形化されません。 注入時間が長すぎることによって引き起こされる球状化の後退は、しばしば妊娠の後退と共存します。 グラファイトが球状化されることを保証する残留Mgの量は、溶鉄の球状化品質を決定します。 MgはOおよびSと強い親和性があります。MgはOと結合してMgOを生成し、燃焼させます。 特にSは、SがMgと結合してMgSスラグを生成すると、液面に浮きます。 液面に浮いた後、MgSスラグ中のMgは空気中のOと結合してMgOを生成して燃焼し、分離したSは再び溶鉄に戻ってMgと結合します。 溶銑中のSはボートのようなもので、常に溶銑中のMgを空中に運び、燃焼させます。これを「復帰現象」と呼びます。 注湯時間が長くなると、溶銑中のMgの残留量はますます少なくなります。 いくつかの情報によると、注入時間の延長に伴い、溶鉄中のMgの燃焼損失は0.004分ごとに1%です。
解決策:何らかの理由で注入時間が長くなる場合は、適切な厚さの絶縁剤を覆って、溶銑と空気の接触を減らし、溶銑で燃焼するMgの量を減らすことができます。 さらに、適切なフォローアップ接種措置を講じて、成長して変形した(成長するとフレークグラファイトになる)グラファイトを分解または切断して、その形状が球形になるようにする必要があります。
15.繁殖不況
金属組織分析により、インキュベーション低下の金属組織写真では、グラファイトボールの数が少なく、ボールの直径が大きく、密度が薄く、球状化レベルが低いことがわかります。 一般に、フェライトの含有量は少なく、パーライトの含有量は多く、炭化物があります。 存在。 接種が減少する理由は、接種剤が少量添加されているか、接種プロセスが完全ではないためです。 マグネシウムの存在は球状化の必要条件であり、接種要素は黒鉛化に参加するための十分条件であるため、球状化処理のみが強調されておらず、高品質のダクタイル鋳鉄を製造することは不可能です。
予防策:追加する接種材料の量を増やします。 バリウムとカルシウムを含む長時間作用型の接種剤を使用します。 二次接種、フローティングシリコン接種、フロー接種などの複合接種対策を講じてください。
16.球状化バッグまたは注入バッグが濡れている
球状化プロセスが溶銑に流されると、水が気化して分解され、水素と酸素が生成されます。 Oは球状化剤中のMgの一部を中和してMgOスラグになり、溶銑中のマグネシウム含有量を減らすだけでなく、鋳物にスラグ穴や細孔欠陥を生じやすくします。
17.オンサイト管理
球状化剤の管理と積み重ねは標準化されておらず、フェロシリコンが混合されている可能性があります。 球状化剤の重量が不正確である、剥離や誤読などがない。例えば、ある工場でのダクタイル鋳鉄の製造品質は非常に安定している。 突然、XNUMXつの炉は夜勤前の球状化が不十分であり、実験室分析のシリコン含有量は基準を超えていました。 調査・分析の結果、地面に散乱したフェロシリコンは日中に清掃された可能性があります。 、球状化剤タンクに分類されます。 また、球状化剤の保存時間が長すぎて保存状態が悪い。 球状化剤の酸化は、球状化効果を弱め、球状化の品質に影響を及ぼします。
結び
日々の仕事では、一生懸命働くことと働かないことは似ていますが、製品の品質の向上と安定化、そしてオペレーター自身の技術レベルの向上には大きな違いがあります。
転載のためにこの記事の出典と住所を保管してください: 不十分な球状化の17の理由と制御
ミンゲ ダイカスト会社 高品質で高性能な鋳造部品の製造と提供に専念しています(金属ダイカスト部品の範囲は主に含まれています 薄肉ダイカスト,ホットチャンバーダイカスト,コールドチャンバーダイカスト)、ラウンドサービス(ダイカストサービス、CNCの機械化,金型製作、表面処理)。カスタムのアルミニウムダイカスト、マグネシウムまたはザマック/亜鉛ダイカスト、およびその他の鋳造要件については、お問い合わせください。
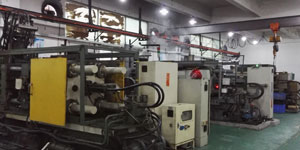
ISO9001とTS16949の管理下で、すべてのプロセスは、ブラスターからウルトラソニック洗濯機に至るまで、何百もの高度なダイキャスティングマシン、5軸マシン、およびその他の設備を介して実行されます。経験豊富なエンジニア、オペレーター、検査官のチームがお客様の設計を実現します。
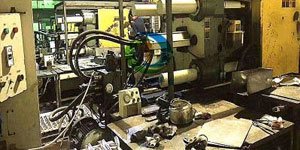
ダイカストの委託製造業者。 機能には、0.15ポンドからのコールドチャンバーアルミニウムダイカスト部品が含まれます。 6ポンドまで、クイックチェンジセットアップ、および機械加工。 付加価値サービスには、研磨、振動、バリ取り、ショットブラスト、塗装、メッキ、コーティング、組み立て、および工具が含まれます。 使用する材料には、360、380、383、413などの合金が含まれます。
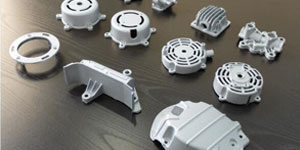
亜鉛ダイカスト設計支援/コンカレントエンジニアリングサービス。 精密亜鉛ダイカストのカスタムメーカー。 ミニチュア鋳造、高圧ダイカスト、マルチスライドモールド鋳造、従来のモールド鋳造、ユニットダイおよび独立ダイカスト、およびキャビティシール鋳造を製造することができます。 鋳物は、最大24インチインチ+/- 0.0005インチの公差で長さと幅で製造できます。
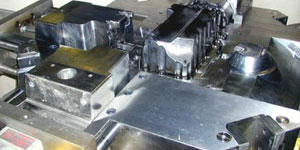
ISO 9001:2015年にダイキャストマグネシウムの認定メーカー。機能には、最大200トンのホットチャンバーと3000トンのコールドチャンバーの高圧マグネシウムダイカスト、工具設計、研磨、成形、機械加工、粉末および液体塗装、CMM機能を備えたフルQAが含まれます。 、組み立て、梱包、配送。
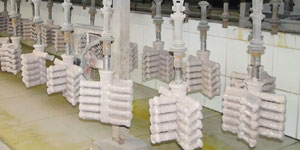
ITAF16949認定済み。 追加の鋳造サービスが含まれます インベストメント鋳造,砂型鋳造,重力鋳造, ロストフォームキャスティング,遠心鋳造,真空鋳造,永久鋳型鋳造、。機能には、EDI、エンジニアリング支援、ソリッドモデリング、および二次処理が含まれます。
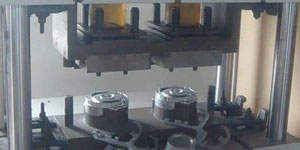
鋳造業 部品のケーススタディ:車、バイク、航空機、楽器、船舶、光学機器、センサー、モデル、電子機器、エンクロージャー、時計、機械、エンジン、家具、ジュエリー、ジグ、テレコム、照明、医療機器、写真機器、ロボット、彫刻、音響機器、スポーツ機器、工具、おもちゃなど。
次に何ができるでしょうか?
∇ホームページに移動 ダイカスト中国
By ミンゲダイカストメーカー |カテゴリ: 役立つ記事 |材料 タグ: アルミ鋳造, 亜鉛鋳造, マグネシウム鋳造, チタン鋳造, ステンレス鋼鋳造, 真ちゅう鋳造,ブロンズ鋳造,キャスティングビデオ,会社の歴史,アルミダイカスト |コメントオフ